Introduction
3D printing, also known as additive manufacturing, has revolutionized numerous industries by offering unprecedented design flexibility and the ability to create custom objects with intricate geometries. From aerospace components to medical implants, the applications of 3D printing are vast and continue to expand. One emerging area where 3D printing holds significant potential is in the design and manufacture of perfume atomizers. Traditionally, perfume atomizers are mass-produced using injection molding or other conventional manufacturing methods. However, 3D printing allows for the creation of unique, personalized designs, enabling greater innovation and customization. But how do these 3D-printed atomizers stack up against their conventionally manufactured counterparts in terms of performance? This article will delve into the key performance indicators (KPIs) for evaluating 3D-printed perfume atomizers and explore the factors that influence their effectiveness.
Key Performance Indicators (KPIs)
To effectively evaluate the performance of 3D-printed perfume atomizers, several KPIs must be considered:
- Spray Quality: This refers to the fineness and evenness of the mist produced by the atomizer. A good atomizer should produce a fine, consistent mist that disperses evenly over the target area. Factors influencing spray quality include nozzle design, internal channel geometry, and the pressure generated by the pump mechanism.
- Spray Pattern: The shape and distribution of the spray pattern are crucial for ensuring efficient and uniform fragrance application. Ideally, the spray pattern should be conical or oval, covering a sufficient area without excessive pooling or dripping.
- Droplet Size Distribution: The size of the droplets produced by the atomizer significantly impacts the olfactory experience. Smaller droplets tend to evaporate more quickly, resulting in a more immediate and intense fragrance release. Larger droplets may lead to a longer-lasting but potentially less subtle scent. An ideal atomizer produces a narrow droplet size distribution with a majority of droplets falling within a specific range.
- Spray Angle: The angle at which the spray is emitted from the nozzle is important for controlling the target area. A wider spray angle covers a larger area, while a narrower angle provides more focused application. The desired spray angle depends on the intended use of the atomizer.
- Spray Volume: The amount of perfume dispensed per spray is a critical factor for determining the longevity of the fragrance and the overall user experience. The spray volume should be consistent and controllable.
- Pump Actuation Force: The force required to depress the pump mechanism should be comfortable and consistent. Excessive force can lead to user fatigue, while insufficient force may result in incomplete atomization.
- Leakage and Durability: A well-designed atomizer should be leak-proof and durable enough to withstand repeated use and handling. Leakage can lead to fragrance loss and damage, while poor durability can shorten the lifespan of the atomizer.
- Material Compatibility: The material used for 3D printing must be compatible with the chemical composition of the perfume to prevent degradation, discoloration, or other adverse reactions.
Factors Influencing Performance
Several factors can influence the performance of 3D-printed perfume atomizers:
- 3D Printing Technology: Different 3D printing technologies, such as Fused Deposition Modeling (FDM), Stereolithography (SLA), and Selective Laser Sintering (SLS), offer varying levels of precision, resolution, and material options. SLA and SLS generally produce smoother surfaces and finer details compared to FDM, which can be advantageous for atomizer nozzle design.
- Material Selection: The choice of material significantly impacts the atomizer’s chemical resistance, mechanical properties, and overall performance. Common materials for 3D-printed atomizers include polymers like ABS, PLA, PETG, and nylon, as well as resins specifically formulated for SLA. The selected material must be chemically inert and resistant to the solvents and fragrances present in the perfume.
- Design Optimization: The design of the atomizer, including the nozzle geometry, internal channel configuration, and pump mechanism, plays a crucial role in determining its performance. Computational fluid dynamics (CFD) simulations can be used to optimize the design for spray quality, spray pattern, and droplet size distribution.
- Post-Processing: Post-processing steps, such as surface smoothing, cleaning, and sealing, can significantly improve the performance and appearance of 3D-printed atomizers. Surface smoothing can reduce surface roughness, which can improve spray quality and reduce leakage. Sealing can prevent perfume from permeating the material and causing degradation.
- Printing Parameters: Printing parameters, such as layer height, printing speed, and infill density, can affect the dimensional accuracy, surface finish, and structural integrity of the atomizer. Optimizing these parameters is essential for achieving the desired performance characteristics.
Challenges and Limitations
While 3D printing offers numerous advantages for perfume atomizer manufacturing, it also presents several challenges and limitations:
- Material Limitations: The range of materials suitable for 3D printing is still limited compared to traditional manufacturing methods. Finding materials that are both chemically resistant and durable enough for perfume atomizers can be challenging.
- Surface Finish: 3D-printed parts often have a rougher surface finish than conventionally manufactured parts, which can affect spray quality and increase the risk of leakage. Post-processing is often required to improve the surface finish.
- Scale of Production: 3D printing is generally more suitable for small-batch production or prototyping than for mass production. The cost per unit is typically higher than for traditional manufacturing methods.
- Dimensional Accuracy: Achieving high dimensional accuracy with 3D printing can be challenging, especially for complex geometries. Variations in printing parameters and material properties can lead to deviations from the intended design.
Comparative Analysis with Conventional Atomizers
When comparing 3D-printed atomizers to conventionally manufactured atomizers (typically injection molded), several key differences emerge:
- Design Flexibility: 3D printing offers significantly greater design flexibility than injection molding. This allows for the creation of unique and personalized atomizer designs that are not possible with traditional manufacturing methods.
- Customization: 3D printing enables mass customization, allowing for the production of atomizers tailored to specific customer preferences or fragrance formulations.
- Cost-Effectiveness for Small Batches: 3D printing can be more cost-effective for small-batch production or prototyping than injection molding, which requires expensive tooling.
- Surface Finish: Injection molded atomizers typically have a smoother surface finish than 3D-printed atomizers, which can result in better spray quality and reduced leakage.
- Material Availability: Injection molding offers a wider range of material options than 3D printing.
- Production Speed: Injection molding is generally much faster than 3D printing, making it more suitable for mass production.
- Durability: Injection molded atomizers are typically more durable than 3D-printed atomizers, due to the higher density and strength of the materials used.
Conclusion
3D printing holds immense potential for the design and manufacture of perfume atomizers, offering unparalleled design flexibility, customization options, and cost-effectiveness for small-batch production. However, challenges remain in terms of material limitations, surface finish, and scalability. To effectively evaluate the performance of 3D-printed atomizers, it’s crucial to consider key performance indicators such as spray quality, spray pattern, droplet size distribution, and leakage. Continued advancements in 3D printing technology, materials science, and design optimization will pave the way for wider adoption of 3D-printed perfume atomizers in the future. As materials become more robust and readily available, post-processing techniques improve, and the speed of printing increases, 3D printing will become a viable and competitive alternative to traditional manufacturing methods for a broader range of perfume atomizer applications.
Frequently Asked Questions (FAQs)
What are the best materials for 3D printing perfume atomizers?
Generally, polymers like PETG, nylon, and polypropylene are good choices due to their chemical resistance and printability. Resins designed for SLA printing can also be suitable, but their compatibility with specific perfume formulations should be carefully evaluated.
How can I improve the surface finish of a 3D-printed atomizer?
Several post-processing techniques can be used, including sanding, polishing, vapor smoothing (for certain materials), and coating with a sealant or protective layer.
Are 3D-printed atomizers safe for use with all types of perfumes?
Not necessarily. It’s essential to ensure that the material used for 3D printing is compatible with the chemical composition of the perfume to prevent degradation, discoloration, or other adverse reactions. It is recommended to test with a small amount of perfume before filling the entire atomizer.
How durable are 3D-printed atomizers compared to conventional atomizers?
Typically, injection-molded atomizers are more durable due to the higher density and strength of the materials used. However, with careful material selection and design optimization, 3D-printed atomizers can be made reasonably durable for everyday use.
Can I 3D print the entire atomizer, including the pump mechanism?
Yes, it’s possible to 3D print the entire atomizer, including the pump mechanism, but it requires careful design and precise printing. Often, the pump mechanism is a separate component that is assembled with the 3D-printed housing.
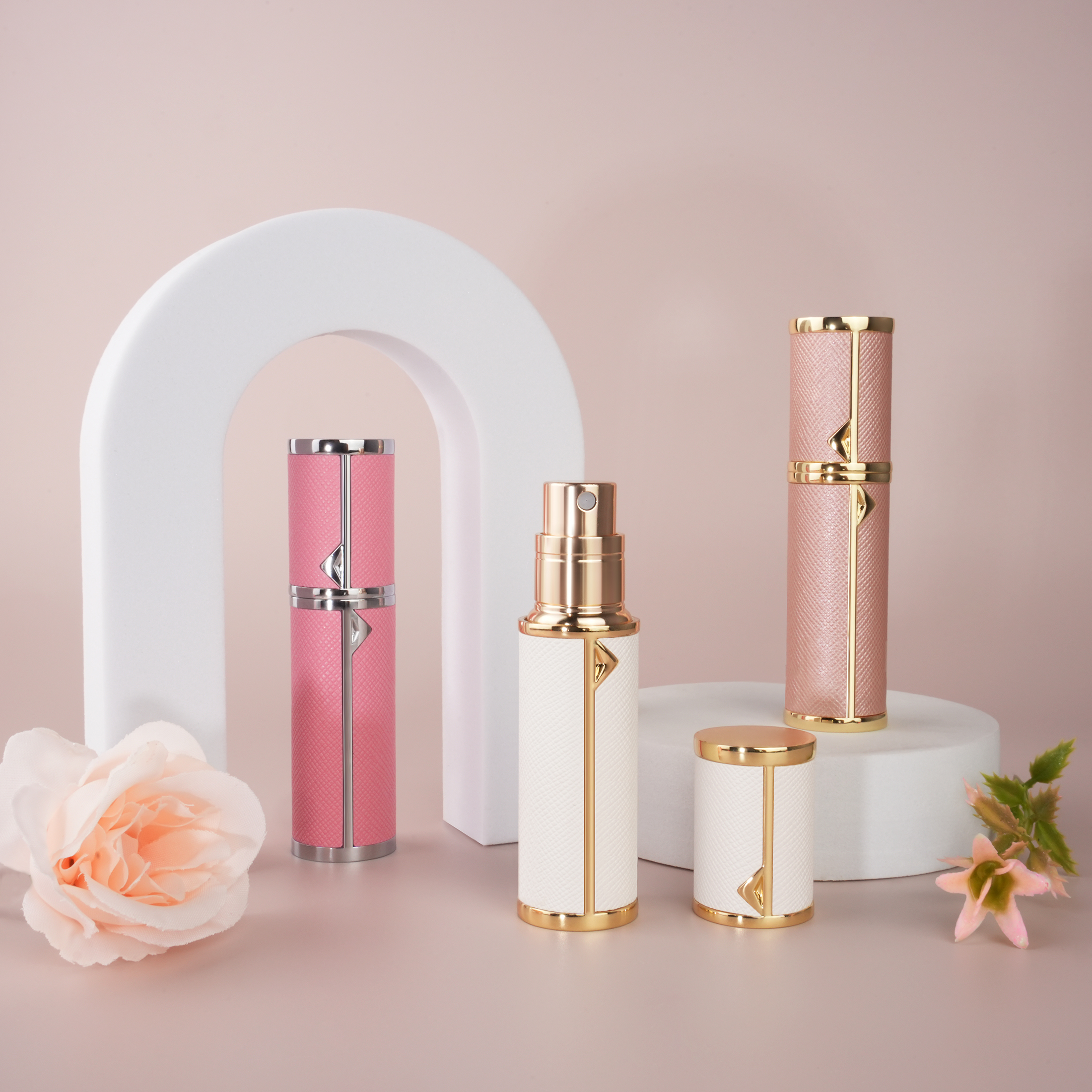
Leave a Reply